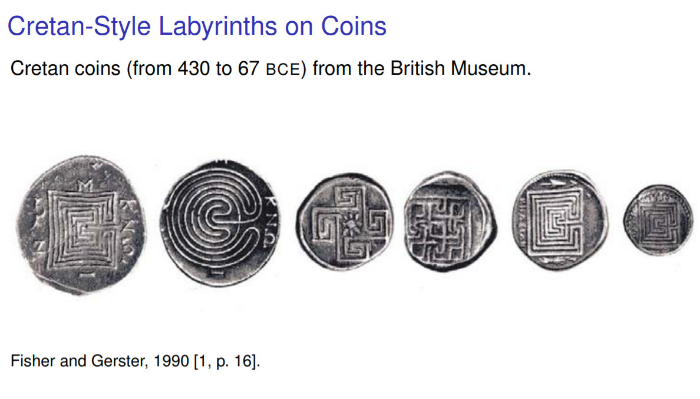
Architecture and Mazes
An overview
Based on Berer, -*A maze allows an objective analysis of process and results. It is a very basic task with simple rules that inherits a considerable challenge for both designers and users (Berer, 1981).[br][br]Mazes are very old and found on many ancient representations, they were used as games, puzzles, and mysteries to be solved. They were represented on temples and walls of different religious buildings all over time.[br][br]As described by Schnabel (2014) explaining the symmetry in mazes as they are built on a symmetrical grid-framework, single, double, vertical, horizontal, and angled cuboids configured the cube following a principle of architectural hierarchy and structure. [br][br][br]
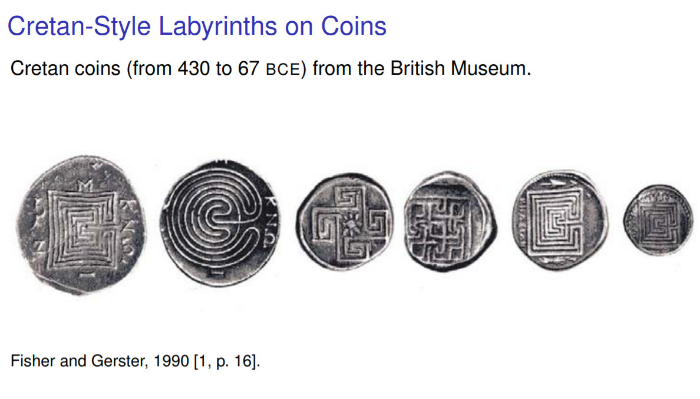
Mazes and technology
[br]As in our book we are presenting mazes with AR there are also mazes with VR as seen by Schnabel (2014), he introduced in his paper mazes in virtual environments. In his study, he compared the first condition[br]was a conventional representation of 3D space with typical 2D architectonic floor-plans. The second and third conditions used digital 3D models, within either Desktop-VE (DVE), interactive models displayed on a PC-Monitor, or IVE, with the help of Virtual Reality (VR) - tools and viewed with a Head-Mounted Display (HMD). He examined which differences make 2D- versus 3D environments on the results of a design process. Eighteen pairs of randomly selected architectural students were asked to design 3D mazes within a[br]symmetrical grid defining four fields in each spatial direction in remote collaborative design sessions.[br][br]The results of[br]his study was that the questionnaires support these findings:[br][list][*]VE, therefore, offers designers a greater 3D understanding of space and volumes[/*][*]Most importantly, the two sets of experiments show that users of VEs do indeed ‘read’ volumes and space better than when working in 2D representations. [/*][*]The results also suggest, unfortunately, that IVE tools are still so limited that the characteristics of the systems inhibit their effective use in design tasks. [/*][/list][br]
References
[sub]Schnabel, M.A. T. U. of H. K. (2014). 3D Maze : Creation and Translation of Abstract Architectural Virtual Environments. [/sub][sub][i]“Second[br]Wave” of ICT in Education: From Facilitating Teaching and Learning to En-Gendering Education Reform[/i][/sub][sub], [/sub][sub][i]June[/i][/sub][sub].[br]https://www.researchgate.net/publication/228591446[/sub][br][br]
What is a Pattern?
Definition
A pattern is some kind of repeated or regular way something is done.[br]The Cambridge Dictionary tells us: "a particular way in which something is done, is organized, or happens". [url=https://dictionary.cambridge.org/de/worterbuch/englisch/pattern]https://dictionary.cambridge.org/de/worterbuch/englisch/pattern[/url][br][br]You can often see patterns in nature in different contexts. They can include all kinds of forms that can be described mathematically such as symmetries, spirals, tesselations, stripes, or even cracks.
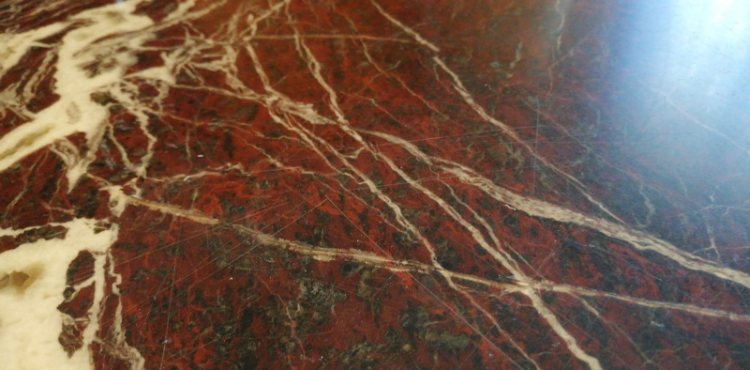
Inclusions in a stone table
Examples of patterns
Patterns can be observed in nature as if they were designed in a specific way. Many plants and animals follow rules creating certain patterns.[br]Examples are honeycombs created by bees or the structure of a fern.[br]Also, objects that are not created by living organisms can follow patterns such as certain rock formations or crystals. [br]Even behaviour or movement can follow a pattern. This can lead to patterns in the design of a city or dancing patterns.
Creating a Maze
Using GeoGebra
You can create your own maze using GeoGebra and send us the link.[br]We then can add your maze to the pool of mazes if we find it suitable!
Start GeoGebra Classic
First, log in to GeoGebra and start GeoGebra Classic.
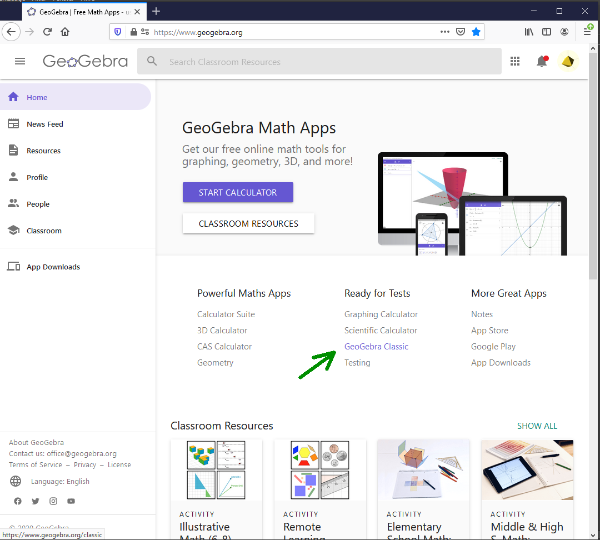
Thinking about your Maze
It is highly recommended to make some doodles or sketches of your maze first.[br]Rules are:[br]walls must be "enclosed bodies" meaning there has to be an inner and an outer wall.
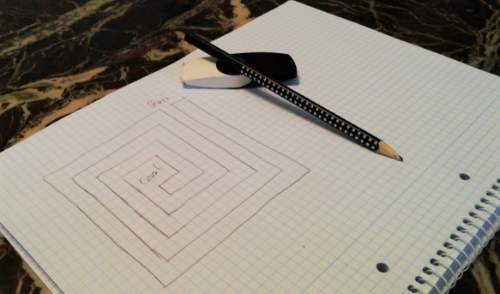
Now go set your scene
For making mazes we recommend selecting the algebraic and graphical view first.[br]You find the menu for this in the top right corner.[br][br]Just so you know, the point "File" contains the save option.
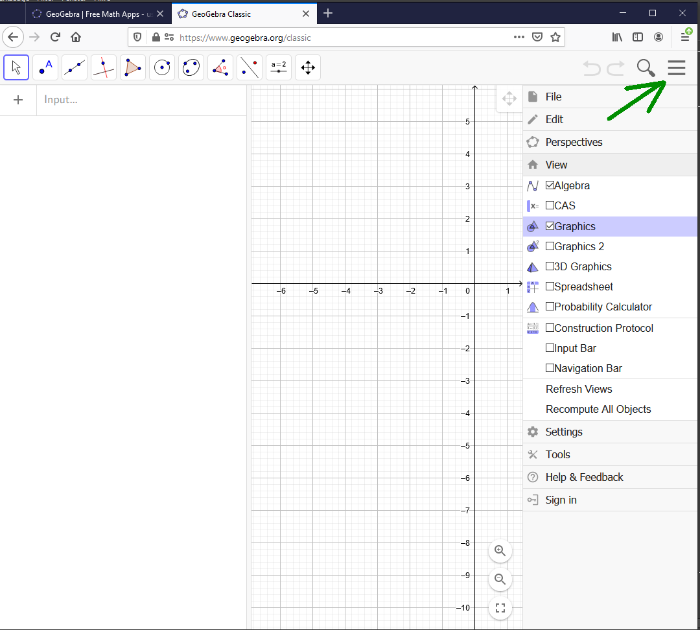
Add Points
Now add points of every corner to Geogebra.[br]You find the points tool on the upper right of the corner.
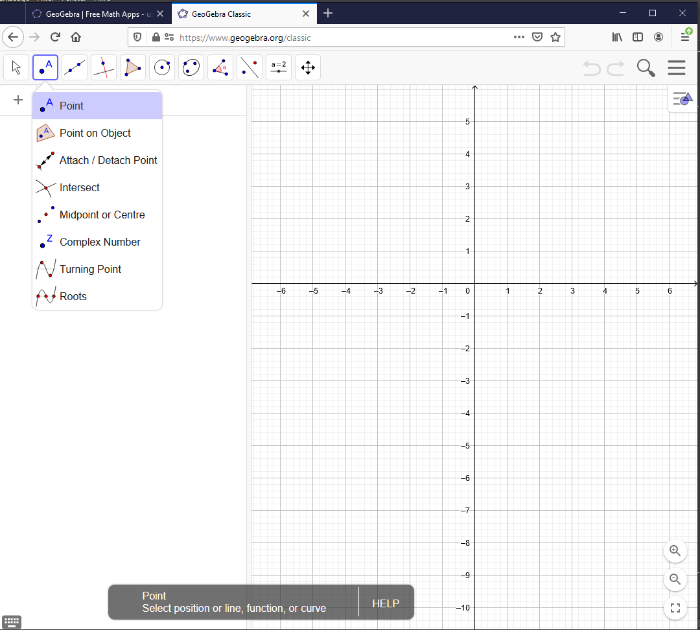
Make it a polygon!
After adding all the necessary points you next should select the polygon tool.[br]Click a point and click all points until you reach the initial point again for a complete polygon.
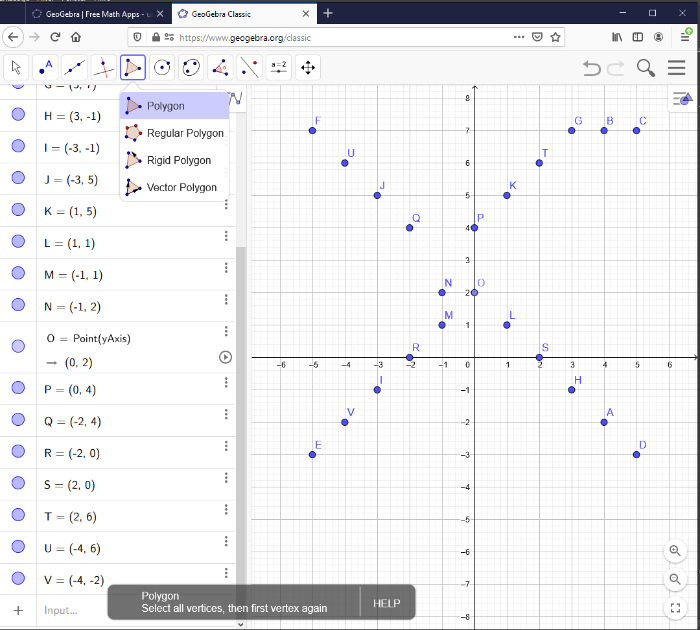
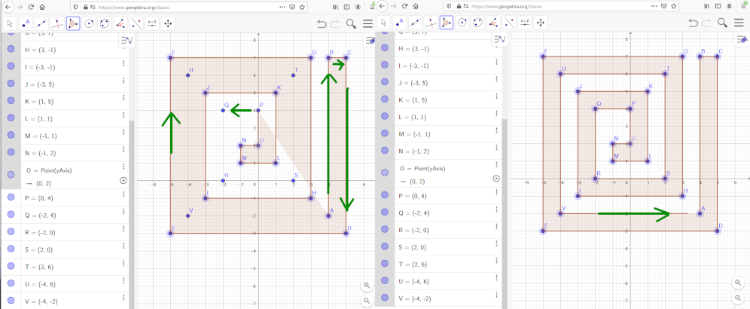
Make it 3D
Now make a 3D prism out of your polygon.[br]To do that you have to choose the 3D view in the menu and select the polygon.[br]Then choose to extrude to a prism in a menu that is now available.[br]Sometimes you need to select the polygon in the 3D view again to have the dialogue pop up for the height.
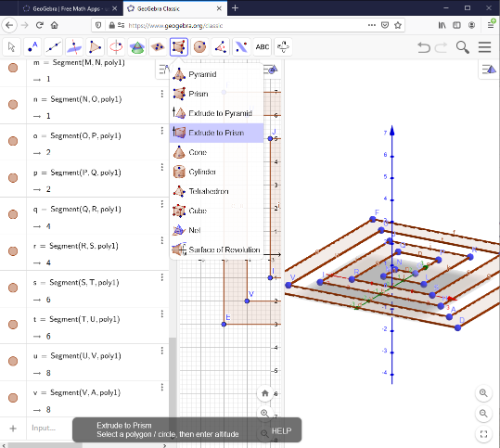
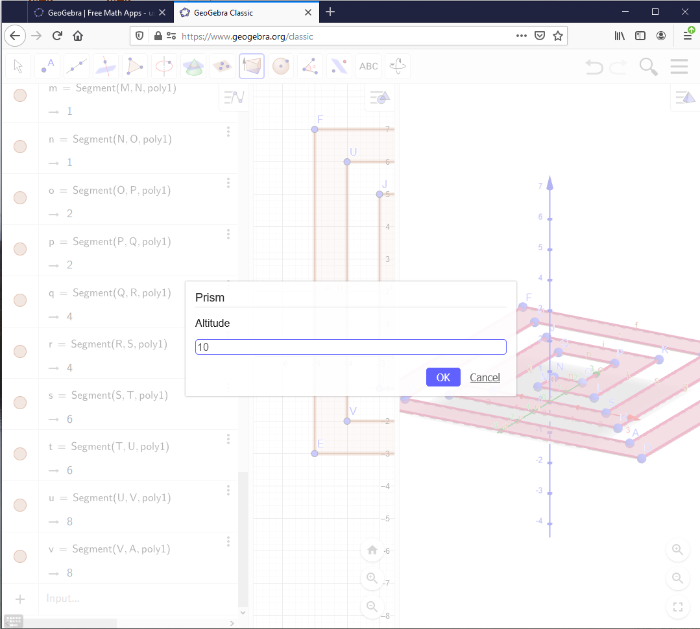
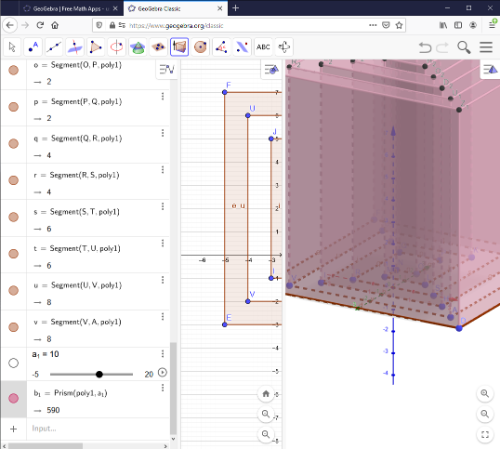
Opacity
To make your maze harder you can choose to change the opacity.[br]First, you can deselect the geometry view to save some screen space the same way you enabled the 3D view. Next, scroll in the algebraic view until you find the prism object describing the entire prism and select ist.[br]Like that, all walls are selected and you can change all their opacities simultaneously.[br]Then, select the settings of the prism object and choose a symbol looking like a square. Here, you find the color options and opacity options.

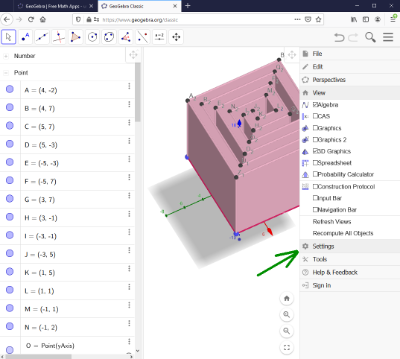
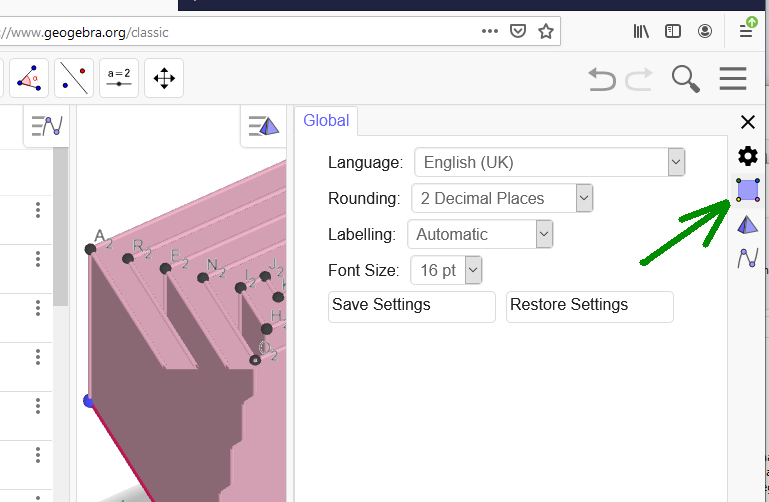
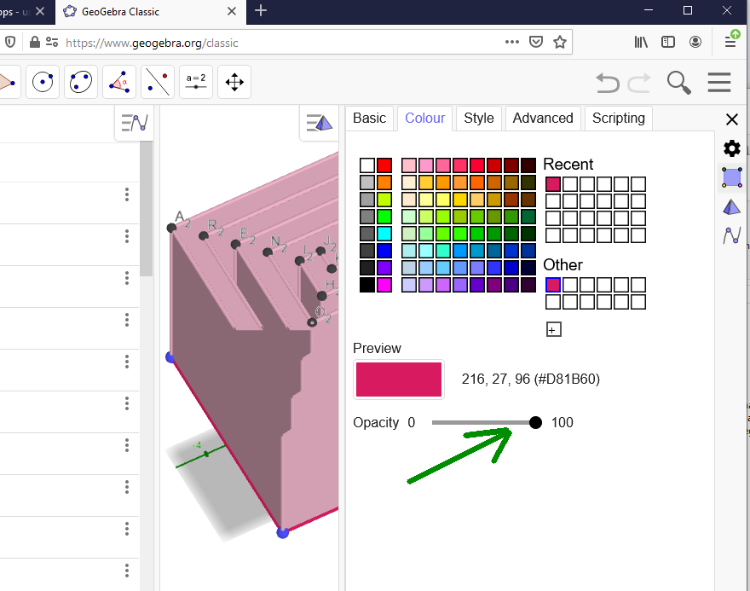
Save your work and send it to us!
Now go to the top right corner again and save your maze under File/Save.[br]In case it worked, your file now gets an ID that is displayed in the URL.[br][br]In case you wish your maze to be included in the puzzles, sent this link to us![br][b]amaze-me@gmx.at[/b]
Share a picture on Instagram
You created your very own cool maze? Take a screenshot and share it with us on Instagram![br][b]#steammaze @geogebraoriginlab[/b]
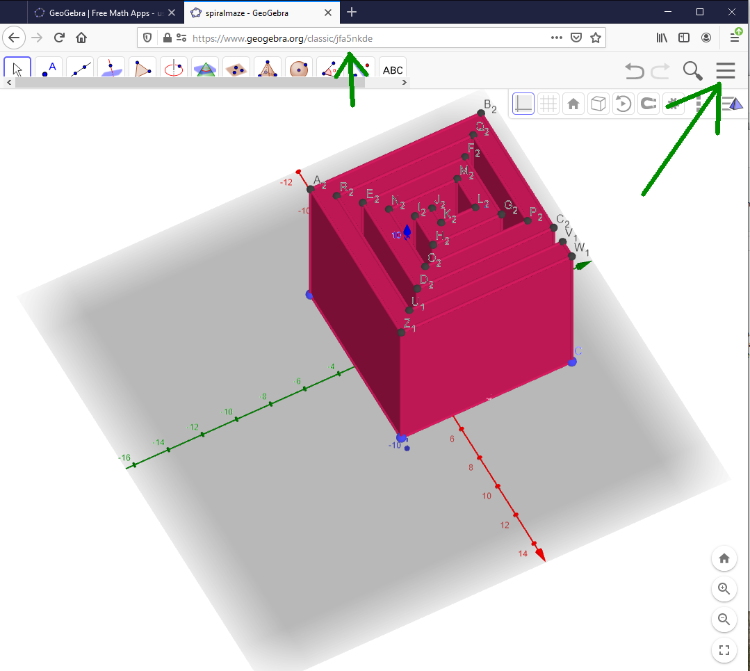
About 3D Printing
What does 3D printing mean?
3D printing is a technology for additive manufaturing. In contrast to eg. CNC milling, there is no material taken away to produce a part but material is added until a part is built.[br]It can be compared a bit to the difference between a sculpture where a person is carved out of a rock like Michelangelos David in contrast to a snowman where snow is collected in balls until a hat and a nose can be attached.[br]Material is usually added in layers, like a cake often consists of layers that are connected by some cream. For 3D printing, the layers can be connected in different ways, regarding on the technology.[br]
How old is 3D printing?
For many people, 3D printing is a very new technology which they only discovered recently. However, the for some surprising truth is that 3D printing is a rather old technology. One technologiy - Stereolithography - was developed in 1981 and patented in 1984. The first program for developing 3D models was available since 1983 meaning it is even older than the World Wide Web which was developed in 1989.[br]In fact, 3D printing is already used for prototyping quite often in the industry. It was just not widely used by end users as of yet.[br][br]
Why is 3D printing getting more popular?
In the year 2009, the patent for the Fused Deposition Modeling technology expired. As a result, enthusiasts especially from the field of mathematics started to develop cheap versions of machines using this technology. The now cheaper machines lead to a dropping of prices from 20.000€ and above to only a few hundred within only a decade for really affordable machines.[br]Other patents expired in the last years allowing more affordable machines as well.[br]Not only did prices get more affordable, also the technologies themselves developed and gained better quality by the advent of using 3D printing for the quick production of items or prototypes. And as 3D printing is now more in the focus, more interesting fields like sophisticated materials or new fields of usage open up.
Technology Overview
Technologies can be cathegorized by their used materials and the way they add each layer of material to existing hardened material. Materials cover powders, liquids, endless filaments, granulates, and more. What they all currently share: a layer of material each is hardened and fused with another layer of material until an entire item can be taken out of the machine.[br][br]
FDM/FFF - adding layers until an item is produced
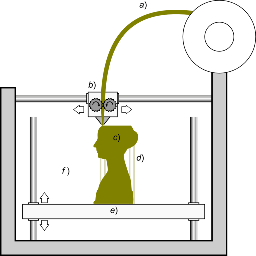
In FFF, a filament which is an endless material string [b]a)[/b] of a thermoplast material is transported to a head that heats up the material [b]b)[/b] and then melts and extrudes it through a nozzle layer per layer [b]c)[/b]. Often, the platform also moves [b]e)[/b]. This technology needs support structures [b]d)[/b] at certain angles to avoid falling layers. Image by Scopigno R., Cignoni P., Pietroni N., Callieri M., Dellepiane M. (2017). "[url=http://vcg.isti.cnr.it/Publications/2017/SCPCD17/DigitalFabricationForCH.pdf]Digital Fabrication Techniques for Cultural Heritage: A Survey[/url]". Computer Graphics Forum 36 (1): 6–21. [url=https://en.wikipedia.org/wiki/Digital_object_identifier]DOI[/url]:[url=https://doi.org/10.1111/cgf.12781]10.1111/cgf.12781[/url].
FDM/FFF - Fused Deposition Modeling/Fused Filament Fabrication
The 3D printing technology which is very affordable and widely available is FDM or FFF which works basically like a glue pistol adding material layer per layer through a nozzle. The technology was developed by S. Scott and Lisa Crump who were part of the company Stratasys. The company Stratasys still holds the patent of the name FDM, thus the RepRap movement - a group of enthusiasts with mostly a mathematical background - created the name FFF which can be used without constraints.[br]This technology uses so called thermoplasts as material. A thermoplast is a material which melts when heated up, is then squeezed through a nozzle and afterwards hardens when cooling down. Often, those [br]thermoplasts are sold as filaments, long strings without any end in one color. [br]As explained before, each melted layer hardens in order to allow another layer to be extruded on top of the old layer. The precision of this technology relies heavily on the layer thickness and the nozzle diameter. The smaller both is, the slower but more accurate the production process is. FDM needs support material for overhangs usually bewtween 30 to 40 degrees.[br]Colors of FDM printed items have the color of the filament used. Most printers use one filament and thus produce items in one color.
SLA - Stereolithography
Developed in 1981 and patented in 1986 by Robert C. Hull, the oldest 3D printing technology uses a material that hardens when exposed to UV light by eg. a laser and is usually a photopolymer - resin is often used today as a material. This technology allows a very high precision. However, it needs to be postprocessed since the sun emits UV light leading to an ongoing hardening process turning it brittle over time. [br]Hull also developed the STL file format. The items produced have the color of the used photopolymer which is usually one color but since it has to have a coating due to the UV hardening, it can be colored afterwards. A variation is spraying photopolymer as droplets through a nozzle hardening the material directly afterwards using a UV lamp. This technology needs support since it is either produced within a liquid or [br]into air.
SLS/SLM - Laser Sintering/Laser Melting
This technology uses a powder, often a variation of Nylon and thus a bit flexible but still very robust, which is applied in layers in some kind of building space, heated up until right before melting together and [br]then shot at by lasers to heat up the material all the way up until they sinter or melt together. Afterwards, the material has to cool down and then can be dug out of the remaining material like a geologist would dig[br] out items from dust. Material only comes in Black, White and variations inbetween so usually, white material is print and the objects are then dyed to achieve colors. Support is not needed since below each layer of material is an existing powder layer of material.
Binderjetting/Inkjet 3D Printing
Just as SLS, Binderjetting uses powder as material, usually gypsum or ceramics but also metal is possible. The material is added in layers, afterwards glued together and then the item is dug out of the remaining [br]powder just as the SLS process - only without a cooldown phase. Furthermore, support is not needed and the majority of unused powder can just be reused.[br]Since the glue can be colored, this technology can produce colorful items.
Simple Spiral Maze
simple_spiralmaze
Examples of Mazes
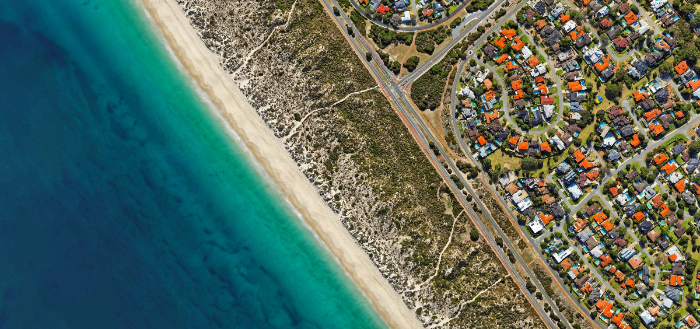
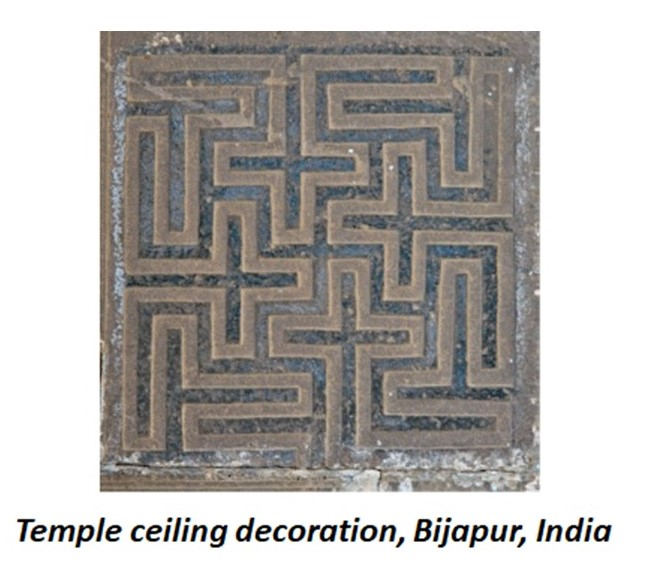
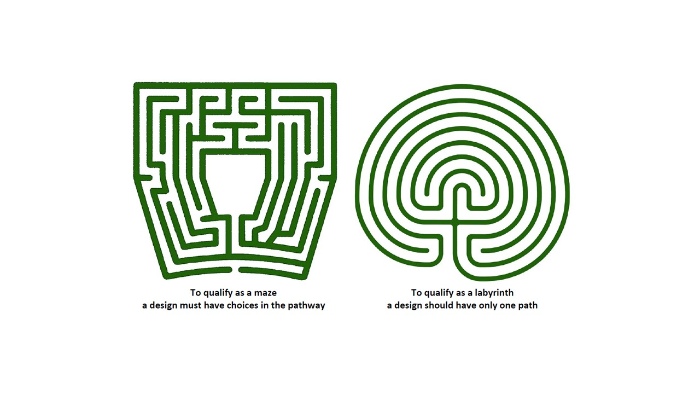
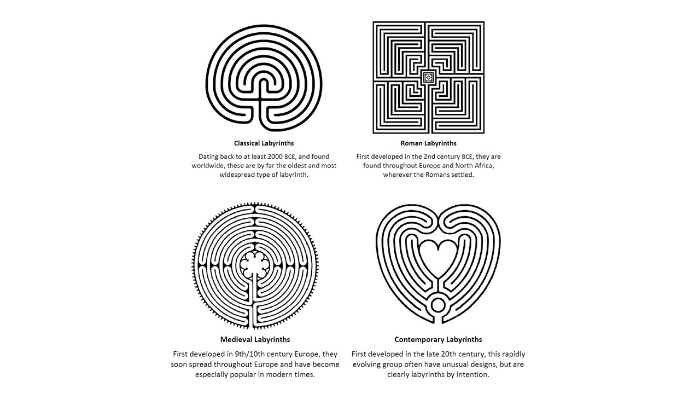
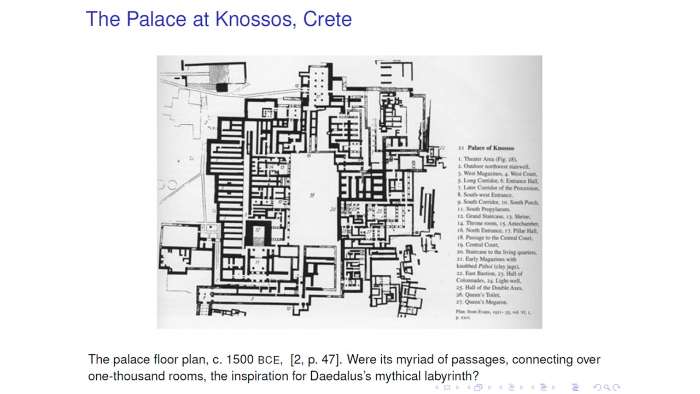
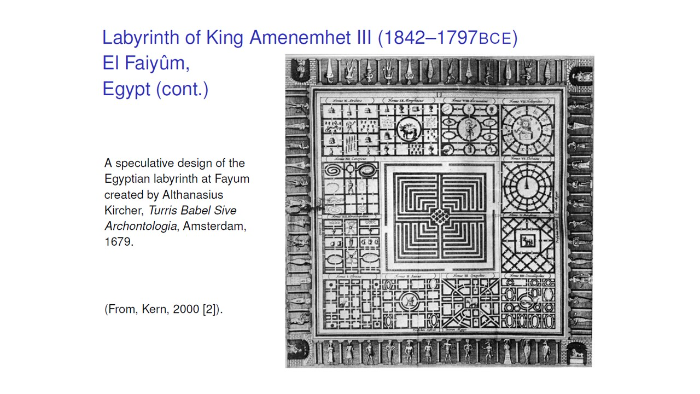
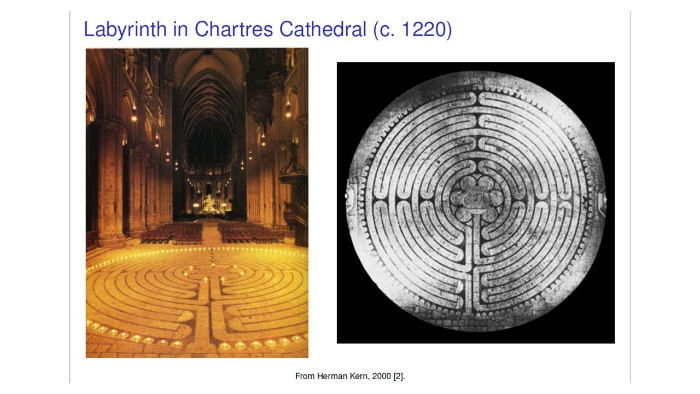
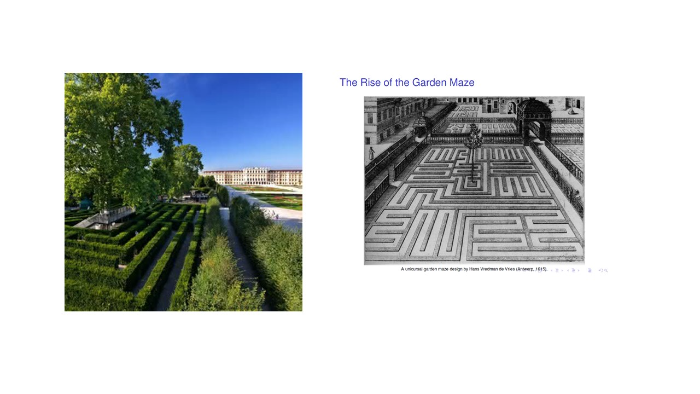
The Team
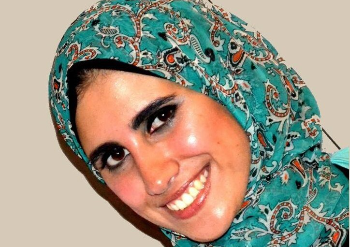
Shereen
Shereen Elbedewy is from Egypt, she studied digital media engineering and technology at the German University in Cairo, 2012. She studied representations of Islamic designs and modern architecture using equations and Boolean functions on Autodesk Maya. She conducted her master’s degree at the JKU in Linz in computer engineering helping visually impaired people to use mathematical notebooks in Mathematica. [br]Her interest shifted to technologies as AR and VR were, she practiced them in educational settings. And that was the connection to her current research at the JKU Linz in the STEAM education department. To connect AR, 3D printing to Architecture, Culture, and History.
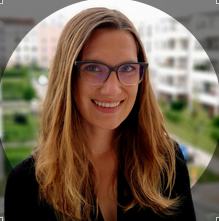
Julia
Julia conducted research on plane-filling curves since 2013. In the course of this research, several puzzles came into being that are now used in this project. Julia is a PhD student, junior researcher, and team member of several ongoing projects at the Institute of Didactics in Mathematics, JKU. She received her Master of Science from Nuremberg Tech in 2018. Her interest is to tear down obstacles for teachers in order to make it easier for them to provide students with positive experiences, especially in STEAM topics. Previously, she has done some research about mathematical curves, leading student groups, and connecting art and STEM topics especially. Her focus is currently shifting towards developing puzzles to teach STEAM-related competencies and support teachers to access technologies.
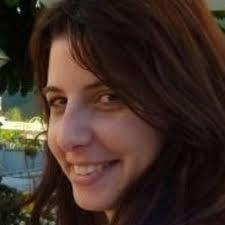
Eva
Eva U. not only has a lot of experience with 3D printing, building, and maintaining printers, she is also familiar with teaching 3D printing to teachers, students, and anyone who is interested in learning about 3D printing. She started to work with this emerging technology professionally in 2013 when she and her husband opened the first 3D printing shop in their hometown, even developing their own Fused Filament Fabrication printers giving her a broad insight into this technology and using binder jetting and stereolithography technologies. Later, she worked as a 3D printing expert at a startup developing a platform for distributed 3D printing orders, gaining even more experience in other printing technologies such as Lasersintering, Lasermelting. During this time she got in contact with many 3D designers from all over the world and mentioned a gap between experienced ones who understand the strengths and weaknesses of the technology as well as those not being able to close the gap between virtual and physical worlds. Moreover, teachers came to her asking for advice on how they could use 3D printing in their classrooms so she started to investigate how teachers could be supported to learn, use, and teach this technology. The idea is to support STEAM education and help raise the understanding of connections between virtual and physical objects.